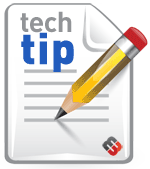
One of the most frequently asked questions raised by engineers, technicians and designers of polymer bonded assemblies, sealants and encapsulants is how to increase the curing speed of a specific polymer composition for a particular application. There is no simple, generally applicable answer, however a number of simple guidelines are available that can substantially help realize the desired objective of increasing productivity by optimizing greater cure speed. First of all, we must be cognizant of the fact that cure speed depends upon quite a number of interrelated variables. These include specifics of the polymer composition’s ingredients, the amount of the compound employed, substrate identification and characterization, application and cure temperatures, time factors, as well as exposure to environmental conditions ranging from aggressive chemicals to mechanical shock and vibration. The following comments should help one arrive at practical, useful solutions.
First of all, it must be kept in mind that the process of curing one or two component polymeric bonding, sealing or encapsulation compounds involves an exothermic, heat emitting reaction. This applies to epoxies, polysulfides, phenolics, polyimides and most urethanes, as well as many other high molecular weight species. The greater the physical amount of the reactants employed, the larger the amount of heat evolved during the curing process. The reverse is true as well: the smaller the quantity of reactants, the lesser amount of heat is evolved. Obviously, the greater the amount of heat evolved, the faster the curing reaction and vice versa. Care must be taken to limit the quantities of reactants in order to avoid building up a reaction temperature which could deleteriously affect other heat sensitive components of the assembly. Cure speed is inversely proportional to reaction time and directly proportional to temperature. For every 20°F (~10°C), the rate of cure is typically enhanced by as much as 20-25%.
To illustrate these phenomena, a typical epoxy adhesive with a 50 mil thick bonding layer will cure much faster than a 3 or 5 mil thick bond. A 3 mil layer may require 40-72 hours at 75°F to obtain a suitable cure state versus 8-12 hours for the thicker layer of epoxy adhesive. Cure of a 1 inch thick shape could well be achieved within 3-4 hours. Increasing the temperature will have the same effect as increasing the amount to be cured. This temperature increase is a simple yet powerful accelerant of the rate of cure. It must be emphasized that quantities of less than 1-2 grams are quite difficult to cure fully even at elevated temperatures. Special technologies are required to obtain adequate cures of such small quantities.
It is generally not recommended to increase the amount of curing agent for the purpose of enhancing the cure rate. Instructions from the manufacturer as listed on the appropriate technical data sheets should be followed carefully. Given a choice, a moderate increase in the curing temperature by only 20-30°F is projected to reduce the cure time by as much as 20-30%. It can be a preferred choice for increasing cure speed in many applications. Technical contact with the manufacturer is recommended to resolve any questions. Master Bond Inc. has experienced technical personnel who would be glad to help if enhanced cure rates are desirable for more cost effective production.